Implement a continuous improvement culture
Kaizen means to change for the better, every day, in all areas of the company, involving all employees. One such area is operator maintenance, where small but continuous improvements can have a significant impact on quality, cost and delivery.
Kaizen helps leaders achieve performance improvements and implement continuous improvement cultures that help them create a sustainable competitive advantage.
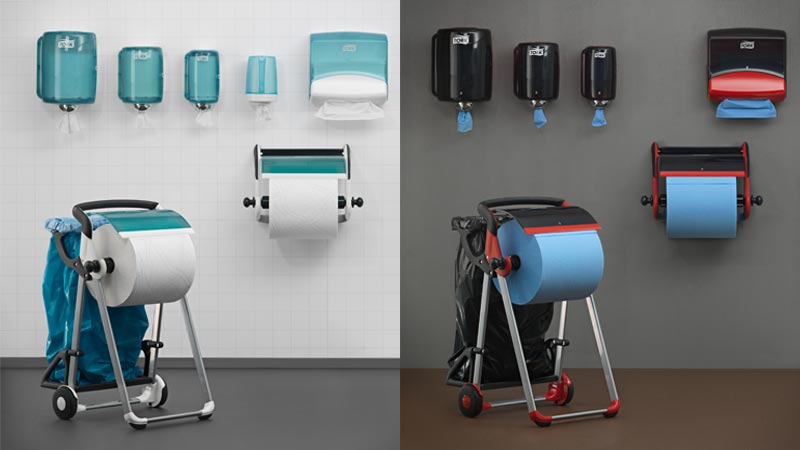
Tips from Jonas Svanäng
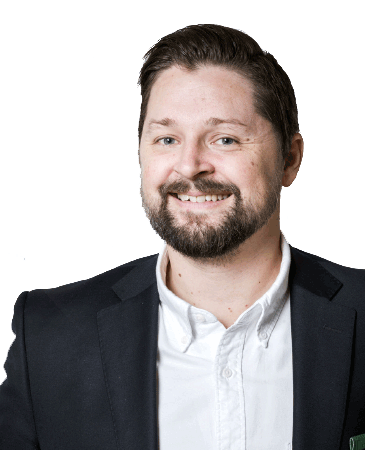
Jonas Svanäng, Kaizen management expert
Jonas Svanäng, learned and studied Lean first hand from improving Toyota’s factories and applied the same learning in 100+ organisations internationally during his time with McKinsey and Reach. Jonas is regularly invited to share his thoughts on kaizen and Operational Excellence at international conferences.
Tip Nr. 1: Focus on small changes
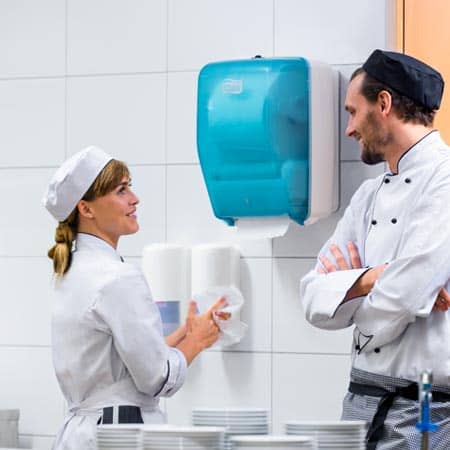
The kaizen approach is to make incremental changes that fit your current operations without having to completely overhaul your processes. Don’t start by asking big and daunting questions like “how can we improve our overall productivity?”. Instead, identify smaller problems and take small, achievable steps towards resolving them.
Improvement ideas will come from going to “Gemba”, a word which in the kaizen methodology refers to the place where value is created for the customer. Bring management to the shop floor to see what’s really going on and where there are opportunities to reduce “Muda” (business/process waste).
That way you can free up time and resources for activities that actually add value.
Look at problems as improvement opportunities. Your goal is to identify root causes of problems and then resolve them together, one step at a time. After a while, these small but continuous changes will take on a momentum of their own and lead to big improvements over time.
Tip Nr. 2: Empower your employees
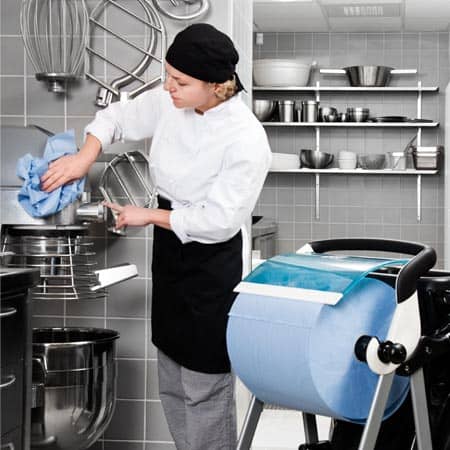
Kaizen is about continuous improvement by everyone, every day and everywhere in the organisation. Your operators are closest to the problems on your shop floor and most probably the ones who know what changes need to be made, but when their suggestions aren’t heard, motivation decreases.
The goal of kaizen is to instil a culture of continuous improvement, through the modification of behaviours. When your company adopts a kaizen mindset, the opportunity to change the place of work and the place where value is really added, will empower your employees.
Strive to create a teamwork environment where everyone is working together to ensure ongoing improvement and encourage your operators to identify problems and make recommendations regarding their work areas.
This not only builds a sense of ownership of their work, it will also improve overall morale and productivity
Tip Nr. 3: Ensure organisational buy-in
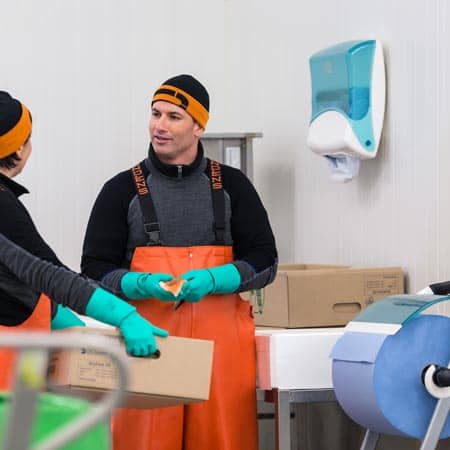
Kaizen is not a one-time fix, but an ongoing process. Which is why you need to engage everyone in the pursuit of improvement, every day, in all areas and departments. And make sure that your organisation understands the importance of kaizen to your bottom line.
Every organisation has issues like breakdowns and quality problems and sometimes there’s a resistance aspect from the shop floor: “We’ve suggested this before but nothing’s happened”, etc.
This makes it important that your employees feel that they have the support they need from management in order to suggest and implement improvements.
To create truly effective and sustainable change, you need to make kaizen an integral part of your leadership. Your leaders are crucial to sustaining a culture of continuous improvement. You need commitment from them on your vision to make sure that they are involved and that they actively support the change in mindset throughout the organisation.
Tip Nr. 4: Speak with data, manage with facts
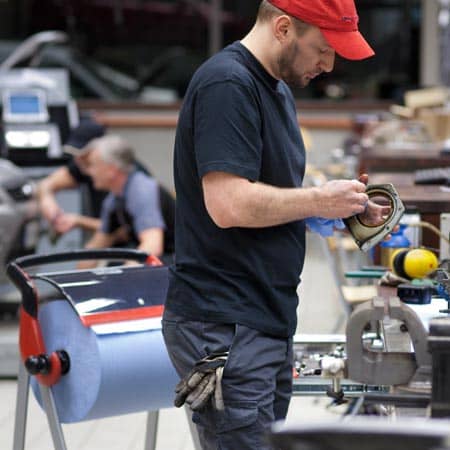
Managers need facts and figures rather than guesses to be able to objectively analyse issues, quantify the benefits of suggested improvements and get buy-in from management. So try to convey to your operators and team leaders the need to speak with data.
Map and quantify your processes to identify Muda and areas for improvement and to provide a benchmark against which future improvements can be measured and quantified.
There is only one way to see what is really happening in your company and why it is happening: you have to change your perspective and “Go to Gemba”.
Don’t just give your opinion on issues; go see what is actually going on by showing genuine interest in the people and the process they work within on a daily basis.
Tip Nr. 5: Cleaning is checking
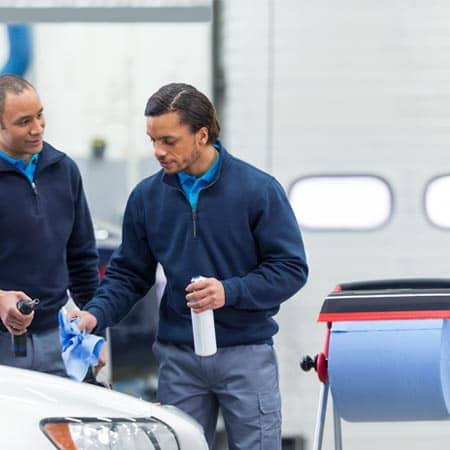
Autonomous Maintenance and Planned Maintenance Routines are pivotal in increasing the overall equipment effectiveness of your plant and its machinery.
In the kaizen system, Autonomous maintenance is “independent” maintenance carried out by the operators themselves rather than by dedicated maintenance technicians. The first step of Autonomous maintenance is basic cleaning.
Research shows that 89% of machine operators believe it is easier to inspect and detect faults on a clean machine.* And when you give your operators the responsibility to keep their equipment clean, they have a better chance of discovering problems before they result in downtime.*
This is an example of how improvement can come from unexpected places. By implementing autonomous cleaning routines, you can increase your bottom line through reducing the downtime of machines, by helping you to proactively:
1. Eliminate leakages
2. Report mature or premature wear
3. Improve access to check points
4. Eliminate sources of dirt and contamination
To facilitate autonomous cleaning routines, and remind operators to carry them out, install Tork cleaning equipment within easy reach of workstations to avoid wasting time walking back and forth to get it.
-
Multipurpose Cleaning Cloth, Biobased W8, White, Tork
-
Multipurpose Cleaning Cloth, Handy Box W7, white, Tork
-
Dispenser for napkins Washstation W6, Tork
-
Kitchen Cloths, W4, White, Premium, Tork
-
Tork Heavy-Duty Cleaning Cloth, white, premium, Tork
-
Portable Centrefeed Dispenser Reflex, Tork
-
Long-Lasting Cleaning Cloth W1-3, Tork
-
Cleaning paper 440 W1, Tork
-
Heavy Duty Cleaning Cloth W4, Tork
-
Heavy Duty Cleaning Cloth W4, Tork
-
Cleaning paper W1/W2, Tork
-
Napkin dispenser, W4, Tork
-
Mobile Dispenser for Napkins/Rollers W1, Tork
-
Mobile Dispenser for Napkins/Rollers W1, Tork
-
Dispenser Napkins/Roller W1, Tork
-
Dispenser Napkins/Roller W1, Tork
-
Reflex Towel Dispenser Mini M3, Tork
-
Portable Dispenser Reflex, Tork
-
Reflex Towel Dispenser M4, Tork
-
Napkin dispenser, W4, Tork
As many as 89% of machine operators agree that “Having robust, professional industrial wiper dispensers placed exactly where I need them would support efficient cleaning and preventive maintenance”*
* Tork research, conducted by Psyma (July 2021)